Industrial Automation
automation
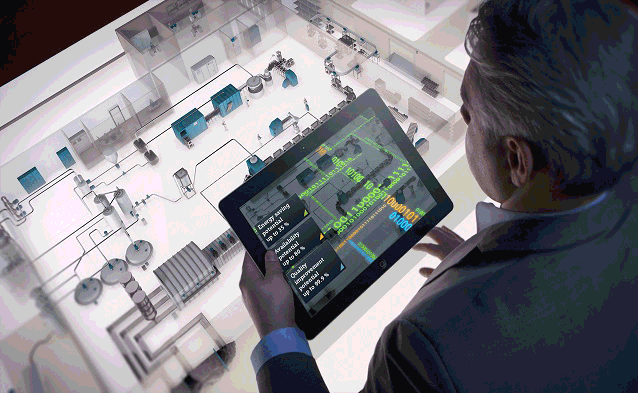
Tuesday, June 13, 2017
Wednesday, June 7, 2017
The future of mining is automated
As global demand increases for resources locked deep within
the earth, the mining industry must adopt processes and technologies that
streamline every step of the process. Automation holds the key to a more
efficient mining industry.
Since the industrial revolution of the mid-1800s, processes
and technologies across every sector of the modern economy have developed at a
rapid pace. From the Bessemer Method of processing steel to the production of
mechanized tools, this era in American history set the pace for the rapid
growth of industry and technology through the 21th century. And as the means to
produce became more efficient, demand for those products increased — and as
demand grew, the methods by which those items were produced advanced further.
Mining is no exception. The steam engine revolutionized both
the digging of new mines and the transportation of product from the mines. Every step of the process —
exploration, discovery, extraction, processing, and distribution — has been
made far more efficient and safer by inventions such as steam-powered mine
hoists, mechanical ventilating devices, shaft excavation systems, and
cementation.
The industrial revolution was no doubt a catalyst for the
development of these inventions, and now the tech revolution is aiming to take
a similar hold on the mining industry. With global demand for an array of
natural resources only increasing, mining companies must work both smarter and
harder to unearth and distribute these commodities around the world. As a
result, the future of mining lies within the technology of automation.
He
challenges confronting the globalized mining industry – now and in the future –
can only be mastered by raising productivity and by reducing operating and
extraction costs. Ever stricter environmental regulations must also be met and
safe working conditions ensured.
Advantages and Disadvantages of Automation in Manufacturing
Automation Advantages
Reduction in
production time – having a machine that is automated definitely
speeds up the production time since no thinking is needed by the machine, there
is better repeatability, and less human error.
Increase in
accuracy and repeatability – when an automated machine is programmed
to perform a task over and over again, the accuracy and repeatability compared
to an employee is far greater.
Less human
error – no one is perfect, and we are all prone to making mistakes.
Which is why a machine that performs repeated tasks is less likely to make
mistakes than an employee.
Less employee
costs – by adding automated machines to an operation, means less
employees are needed to get the job done. It also indicates less safety issues,
which leads to financial savings. With having less employees, there are
numerous costs that are diminished or reduced such as payroll, benefits, sick
days, etcetera.
Increased
safety – having automated machines means having less employees who
perform tasks that can be dangerous and prone to injury, which can make the
work environment safer.
Higher volume
production – investing in automated equipment creates a valuable
resource for large production volumes, which in turn, will increase profitability.
Automation
Disadvantages
Less
versatility – by having a machine that can perform a certain task
limits to the flexibility and variety of tasks that an employee could do.
More
pollution – different types of machines operate using motor which may
require gases or chemicals in order to operate. This can cause an increase in
pollution in the workplace.
Large initial
investment – automated machines can be one of the most costly operating
costs for a company. With automated machines running anywhere between thousands
and millions of dollars depending on the type and degree of automation.
Increase in
unemployment – by increasing the amount of automation, there are less
employees required causing high unemployment rates.
Unpredictable
costs – there can be several unpredictable costs that may exceed the
actual cost saved by the automation itself. Some of these costs could include
research and development costs of automating a process, preventative
maintenance costs, and the cost of training employees to operate automated
machines.
What is Industrial Automation?
Industrial
automation is the use of control systems, such as computers or robots, and
information technologies for handling different processes and machineries in an
industry to replace a human being. It is the second step beyond mechanization
in the scope of industrialization.
The word
‘Automation’ is derived from ancient Greek words of Auto (means self)
Matos (means moving). Thus, a mechanism move by itself or self dictated is
called automation. As compared with manual systems, automation systems provides
superior performance in terms of precision, power and speed of operation.
Industrial
automation is the use of control devices such as PC/PLCs/PACs etc. to
control industrial processes and machinery by replacing as much as possible
labour intervention and dangerous assembly operations with automated ones.
In industrial
control a wide number of process variables such as temperature, flow, pressure,
distance, and liquid levels can be sensed simultaneously. All these variables
are acquired, processed and controlled by complex microprocessor systems or PC
based data processing controllers.
Subscribe to:
Posts (Atom)